
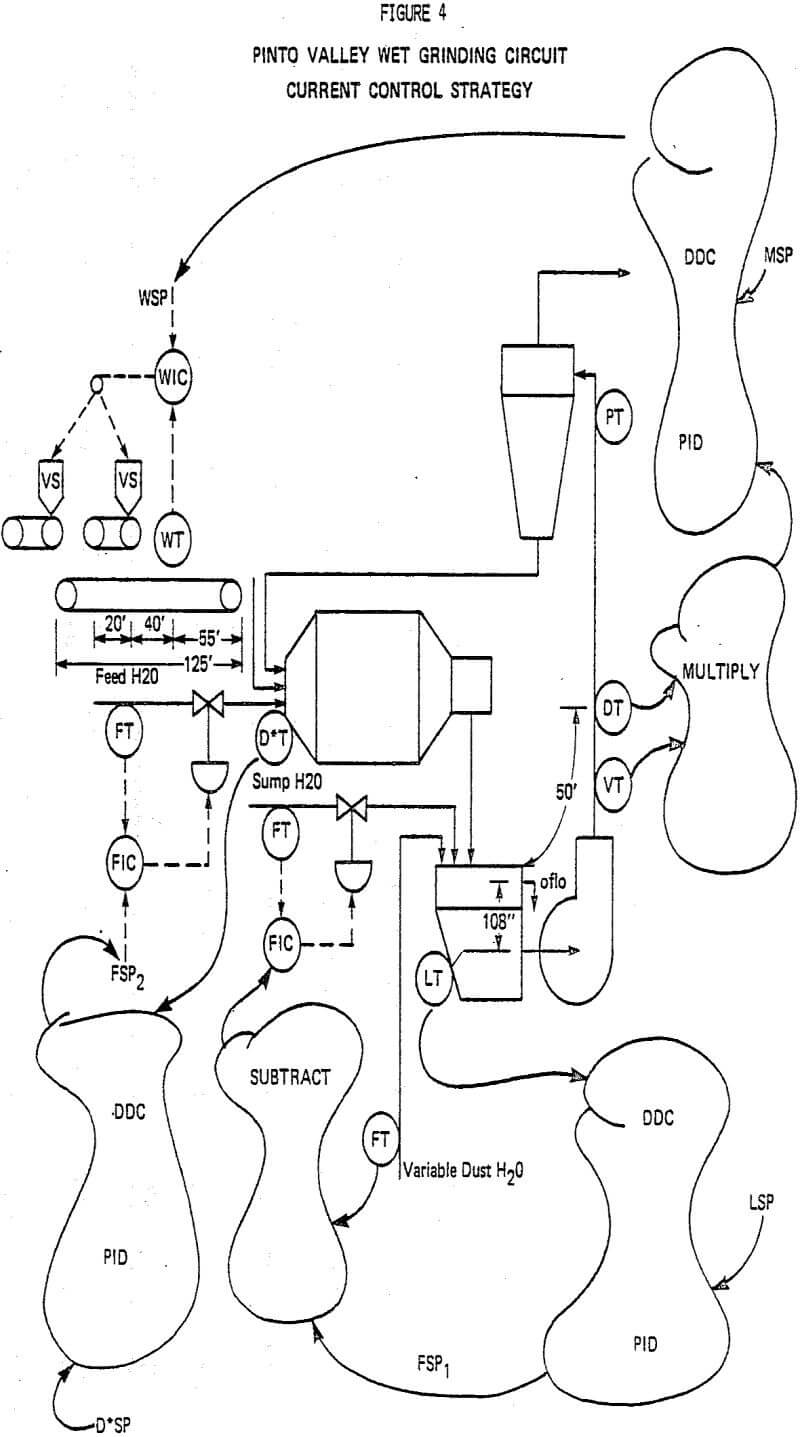
Due to the high gradient, the attractive force is strongest closer to the drum making it most effective when utilized with a relatively low material burden depth on the drum surface and, thus, a lower unit capacity. The poles are placed together minimizing the intervening air gap to produce the high surface gradient. Several identical agitating magnetic poles comprise the element. The high-gradient element, as the name implies, is designed to produce a very high field gradient and subsequently a high attractive force. A typical axial circuit is shown in Figure 3. This configuration typically does not provide a sufficient field strength or gradient for the recovery of paramagnetic minerals at high capacities. This type of drum is simple in design and can be effective for low-intensity applications such as the recovery of ferrous metals and magnetite.

WET GRAVITY CIRCUIT SERIES
The standard magnetic drum configuration consists of series of axial poles configured with an alternating polarity. The magnetic circuit may consist of one of several designs depending on the application. Permanent magnetic drum separators have undergone significant technological advancements in recent years. The magnetic material discharges from the drum shell when it is rotated out of the magnetic field. The magnetic material is attracted to the drum shell by the magnetic circuit and is rotated out of the non-magnetic particle stream. When material is introduced to the revolving drum shell (concurrent at the 12 o’clock position), the non-magnetic material discharges in a natural trajectory. The magnetic circuit is typically comprised of several magnetic poles that span an arc of 120 degrees. The magnetic drum separator consists of a stationary, shaft-mounted magnetic circuit completely enclosed by a rotating drum. These separators are effective in treating process streams containing a high percentage of magnetics and can produce a “clean” magnetic or non-magnetic product. Permanent magnetic drum separators combine the attributes of a high-strength permanent magnetic field and a self-cleaning feature. The CTB series is counter-rotation tank style, it is designed for handling minerals with particle sizes from 0-0.5 mm, especially for mineral with particle size from 0-0.15 mm.The CTN series is counter-current tank style, it is designed for handling minerals with particle sizes from 0.6-6 mm.The CTS series is concurrent tank style, it is designed for handling minerals with particle sizes from 0-6 mm.although hematite (Fe2O3) and siderite Fe2CO3 can be roasted to produce magnetite and hence give good separation in low-intensity machines. The principal ferromagnetic mineral concentrated in mineral processing is magnetite (Fe3O4).

Work has also shown that such separators have maximum field strengths on the drum surface of less than 0.3 T. For low-intensity drum separators used in the iron ore industry, the standard field, for a separator with ferrite-based magnets, is 0.12 T at a distance of 50 mm from the drum surface.

Low-intensity separators are used to treat ferromagnetic materials and some highly paramagnetic minerals. Minerals with ferromagnetic properties have high susceptibility at low applied field strengths and can therefore be concentrated in low intensity (<~0.3T) magnetic separators.
